Coal Processing and Slurry Fuels
The Szego Mill excels in simultaneous grinding, beneficiation and production of coal-slurry fuels. A patent was granted for simultaneous grinding and beneficiation of coal with oil and water in the Szego Mill. In the mill, ash is liberated from coal and enters the water phase, and coal is reduced in size and forms agglomerates in the oil phase. The oil phase is then separated from the water phase, resulting in a stable coal slurry fuel.
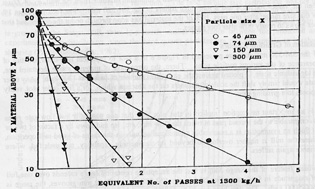
Grinding performance (% above size) vs number of passes for coal at 1300 kg/h in the SM320 mill
Reactivation of sorbent for capture of sulfur from coal combustion
Limestone is added to fluid bed coal burners to capture sulfur, producing compounds which end up in the ash. The limestone becomes deactivated before all of it is consumed due to reaction at the particle exterior. It can be reactivated with grinding and hydration, and this can be done in one step using the Szego Mill, as demonstrated in pilot scale work by Natural Resources Canada. Use of limestone for sulfur capture was 18% lower, which represents a significant cost reduction.
03102607 Advanced fluidized bed combustion sorbent reactivation technology
Anthonv. E. J. et al. Industrial & Engineering Chemistrv Research. 2003. 42, (6),1162-1173.
A new technique for simultaneous grinding and hydrating of fluidized bed combustion (FBC) bottom ash was developed. This method was effective in hydrating’the CaO component of’ the ash, so that the sorbent is reactivated. Careful control of water levels is required to prevent energy demand increases for grinding. No problems associated with the potentially exothermic reaction of water with FBC bottom ash were observed during grinding. When excess water (over that required by hydration) is used, the resulting material is a slurry and, while quantity conversion of CaO in the solids is achieved, using the slurry for the sorbent would require a redesign of the limestone feed system. Therefore, coal or unreacted ash is added to the mixture after grinding.
The resulting dry product contains the spent bed material in a completely hydrated form. The reactivated ash produced was evaluated for sulfur capture using thermogravimetric analysis, and a CFBC pilot plant. Conversion rates of almost 100% are achieved for ash after grinding hydration. An industrial demonstration of the technology has supported its viability with no decrease in sulfur capture, while limestone requirements decreased by 18%. The economic implications of the industrial applicability of the technology are outlined in a case study using the Point Aconi CFBC unit. Decreased limestone usage is calculated to net savings in the order of $500000/year.
The project is calculated to have an equity payback of < 1 year.