Products
Optimized & Industry-ready Solutions
Designed for flexible operation with minimum energy use..
The Szego Mill features unique, proprietary roller mill technology developed by General Comminution Inc. and the University of Toronto over the past 30 years. The mill has very high specific capacity and low energy consumption. It can operate dry, with air sweeping, or wet, and can process slurries and thick pastes. It is suitable for materials of hardness up to 5 on the Mohs scale. Fine particle sizes of 1 to 10 μm can be achieved
Mill Characteristics
- High capacity relative to equipment size
- Dry and wet grinding
- Slurry and paste grinding
- Flexibility in operation
- Combined operations and processing
- Low energy consumption
- Low capital cost
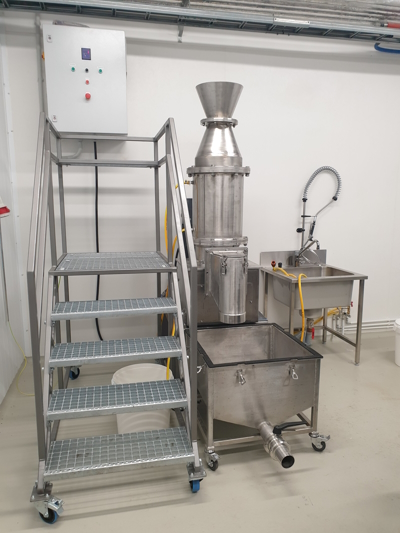
Our Innovations
How The Mill Works
Szego Mill Technology
The Szego Mill consists of rollers with helical ridges and grooves that rotate inside a vertical cylinder called the stator (see diagram). The rollers are free to move in the radial direction, and grinding takes place between the ridges of the rollers and the stator.
The number, diameter, and length of the rollers varies with the mill (stator) diameter, which is incorporated in the mill designation, for example, the SM-320 mill has a stator with an inside diameter of 320 mm. This mill has four 110 mm diameter rollers with a height of 400 or 600 mm.
The Szego Mill is suitable for both dry and wet grinding, and has the ability to process thick pastes. The material to be ground is fed continuously by gravity, or pumped into a top feed cylinder. As it moves down the cylinder, it is subjected to crushing and shearing between the roller ridges and the stator. The grooves aid transport of pasty material through the mill. Ground product is discharged at the bottom. Crushing force is created mainly by the radial acceleration of the rollers, and shearing action is induced in wet grinding by high velocity gradients between roller ridges and the stator.
Grinding forces can be controlled by the speed of rotation and the mass of the rollers.
The rotational speed of the central shaft of the roller assembly is adjustable, and determines the roller peripheral speed. The quality of the product after one pass through the mill is determined by the number, length and diameter of the rollers, the feed rate, the angular velocity, and the characteristics of the material being ground.
An important feature of the Szego Mill is the ability of the roller grooves to aid the transport of material through the mill, thus providing a means to control the residence time, the number of times material is compressed, and, hence mill capacity and product size distribution. This transporting action is particularly important with materials that do not flow readily by gravity, such as pastes and sticky materials.
The ridge/groove size ratio can be changed to increase or decrease the effective pressure acting on the particles. The common groove shapes are rectangular and tapered; the latter will decrease the chance of particles getting stuck in the grooves, as will wide-grooved rollers.
Szego Mill diagram
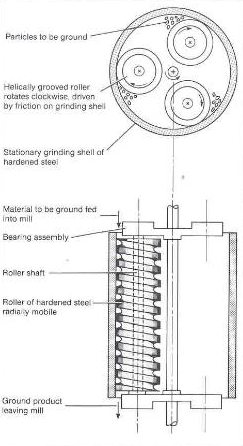
The operating variables for the mill are the material feed rate, its consistency (percentage of solids, if wet), and the rotational speed of the rotor.
Typically, the rotational speed is between 400 and 1200 rpm, depending on mill size, which translates to roller peripheral velocities of 6 to 10 m/s.
The mill is characterized by high capacity per unit volume and modest power consumption. It is very versatile; in wet grinding it can handle highly viscous materials such as thick pastes, i.e., high solids concentrations, without extreme loss of efficiency. Within limits, not only particle size but also particle shape can be controlled, for example, from granular to flaky.
Szego Mills are available in laboratory (160 mm diameter) and pilot (220 mm) sizes, as well as in small industrial sizes (320 and 500 mm) capable of throughputs up 10 tonne/h. Compared to a ball mill, the throughput per unit mill volume is of the order of 30 times higher, and the specific power consumption is typically 30% lower.
While the Szego Mill is a compact and efficient grinder for many applications, a special niche is wet grinding at high solids loadings. A toothpaste-like consistency appears to give the best grinding efficiency.
Size reduction from 6 mm to below 10 microns can be achieved. Grinding can be combined in one step with high energy mixing, leaching, beneficiation, and chemical reaction in open, closed and locked-cycle circuits.
Szego Mill model, size and capacity
Model Number | Power (kW/hp) | Capacity of Dry Solids | Top Feed Size (mm) | Weight (kg) | Dimensions H x L x W (mm) |
SM160/160 | 2.2 / 3 | 20 – 300 | 3 | 100 | 615 x 695 x 315 |
SM220/300 | 15 / 20 | 100 – 1 500 | 5 | 500 | 970 x 900 x 480 |
SM280/280 | 15 / 20 | 100 – 2 000 | 5 | 600 | 2 216 x 1 555 x 2 000 |
SM320/400 | 22 / 30 | 200 – 3 000 | 6 | 700 | 1 380 x 1 287 x 686 |
SM320/600 | 30 / 40 | 200 – 4 000 | 6 | 850 | 1 380 x 1 287 x 686 |
SM500/900 | 56 / 75 | 300 – 7 000 | 10 | 1 900 | 2 378 x 1 775 x 1 142 |
Need Help With Easier Industrial Solutions? We Are Experts!
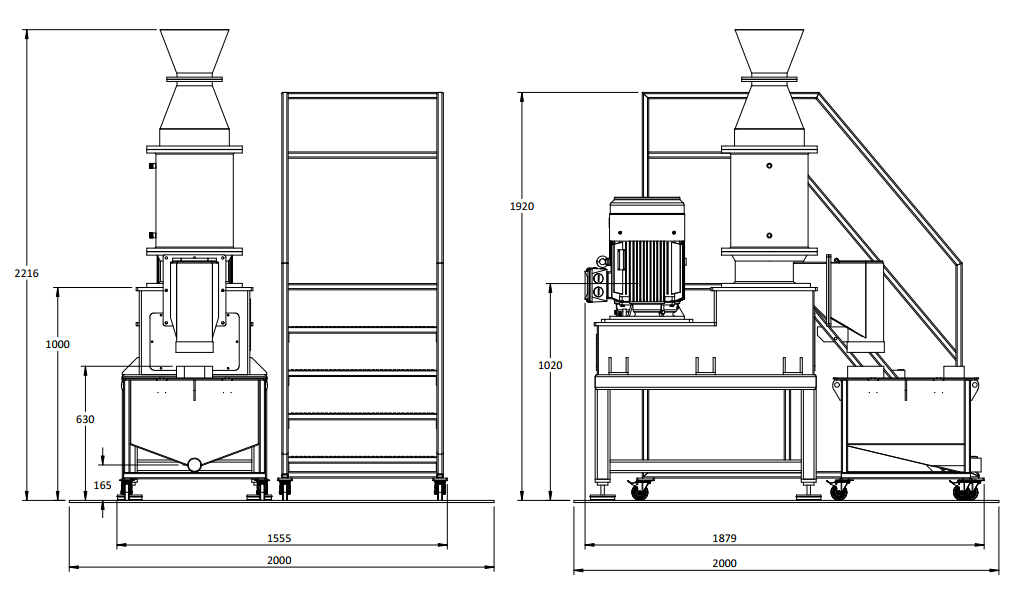
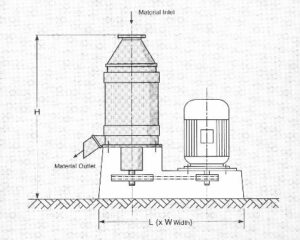
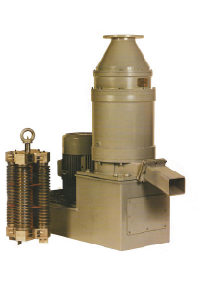